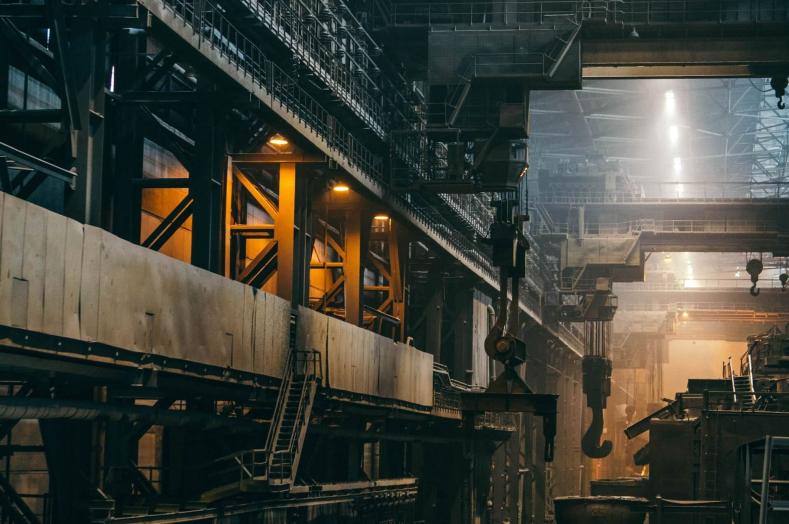
Bei der Kapazitätsplanung geht es darum, Ihre laufenden und anstehenden Projekte zu bewerten und sicherzustellen, dass Ihre Projektorganisation über ausreichend Zeit, die notwendigen Fähigkeiten und die physischen Ressourcen verfügt, um die Projektziele zu erreichen.
Doch wie plant man Kapazitäten, wenn Projekte aufgrund von Engpässen ins Stocken geraten? Aufgrund von geopolitischen Spannungen, Lockdowns und erhöhter Nachfrage können benötigte Materialien oder Komponenten häufig nicht mehr rechtzeitig oder gar nicht geliefert werden.
Dies kann jedoch auch als Chance für einen vielversprechenden Richtungswechsel der Unternehmensstrategie verstanden werden.
Gründe für Engpässe in der Lieferkette
Stark von Rohstoffen oder ausgelagerten Komponenten abhängige Projekte können aus folgenden Gründen ins Stocken geraten:
-
Mangelnder Zugang zu Produktionsanlagen
-
Verspätete Lieferung von Materialien
Die weltweite Halbleiterknappheit verschärfte sich mit der Covid-19-Pandemie. Dies liegt daran, dass viele Hersteller als Reaktion auf die schwankende Nachfrage Chips zurückhielten. Lockdowns, vor allem in China, führten außerdem zu einem erheblichen Rückgang der Chip-Produktion, was den Nachfrageüberhang noch weiter dramatisierte.
Für die Automobilhersteller war dies eine besonders schlechte Nachricht, da in einem einzigen Auto bis zu 3.000 Halbleiter verbaut sein können. Ford, Mercedes und Jeep mussten ihre Produktion stoppen oder drosseln.
Trotz der Gefahren für die Überlebensfähigkeit von Unternehmen durch solche Engpässe, können die Verwerfungen in den globalen Lieferketten auch klare Chancen bieten. Vor allem Automobilhersteller können Zulieferer für Bauteile ersetzen, um beispielsweise ein Armaturenbrett zu bauen, das nicht dieselben Unterkomponenten benötigt.
Standortwechsel
1. Standortverlagerungen
Bietet ein Land nicht (mehr) die richtigen Voraussetzungen für die Produktion, ist es sinnvoll, diese an einen anderen Standort zu verlagern. Dabei müssen jedoch zwei zentrale Voraussetzungen gegeben sein:
- Zugang zur Infrastruktur. Die Nähe Ihrer Produktionsstätte zu zentralen Verkehrsknotenpunkten sowie zu Top-Kunden ist entscheidend. Die Wahl des richtigen Standorts hat Auswirkungen auf Ihre Liefer- kosten sowie auf Ihren Zugang zu Materialien auswirken.
- Verfügbarkeit von Fachkräften. Hier geht es um die Planung der Mitarbeiterkapazitäten, da Sie möglicherweise neue Mitarbeiter für den neuen Standort benötigen. Sie könnten aber auch auf die Arbeitskräfte bestehender Produktionsstätten zurückgreifen. Auch dies kann die Produktionsprozesse reduzieren.
Ein Standortwechsel bedeutet jedoch in der Regel eine Verlängerung der Vorlaufzeiten. Wenn Sie sich also für diese Option entscheiden, sollten Sie sich auf einige Ausfallzeiten und eine Anpassung der Gewinnprognosen einstellen.
2. Wechsel der Zulieferer
Bei Produkten, die auf Materialien und Komponenten von internationalen Lieferanten angewiesen sind, kann es zu längeren Lieferzeiten oder gar zu Lieferausfällen kommen.
Als Reaktion könnten Sie den Zulieferer wechseln. Bei dessen Wahl können geografische sowie politische Aspekte entscheidend sein. Zudem müssen Sie zwei wichtige Punkte prüfen:
Kosten. Der Mehrwert, der Nachfrage nachkommen zu können, und die Investitionen, die bei einem Zuliefererwechsel getätigt werden müssen, müssen genau gegeneinander abgewogen werden. Zudem müssen Sie sämtliche Verträge mit dem aktuellen Zulieferer prüfen. Ein Lieferausfall bedeutet nämlich nicht zwingend, dass gegen den Vertrag verstoßen wurde. Beachten Sie in diesem Kontext auch die Kosten für den Überbrückungszeitraum, bis der neue Zulieferer das Produkt liefern kann. Gegebenenfalls ist auch eine temporäre Preisanpassung einem Zuliefererwechsel vorzuziehen.
Personal. Wenn Sie einen Wechsel zu einem regionalen Zulieferer in Betracht ziehen, was in einem volatilen Politklima wie dem aktuellen eine sehr gute Lösung sein kann, müssen aber in jedem Fall auch der derzeitige Fachkräftemangel sowie die Pläne zu dessen Reduzierung berücksichtigt werden.
„Supplier diversification and relocation can be costly and impractical for highly complex products. And holding more inventory and building redundant capacity could create inefficiencies in many industries.“ – die Weltbank
Diese Entscheidung dürfen Sie keinesfalls leichtfertig treffen. Sie müssen abwägen, ob die derzeitigen Lieferverzögerungen langfristig oder nur von kurzer Dauer sind.
3. Produktanpassung
An dieser Option scheiden sich die Geister. Für viele Unternehmen kann sie bedeuten, dass sie zurück ans Reißbrett müssen.
Sie kann aber auch einen nachhaltigeren Weg zur Erfüllung künftiger Anforderungen bieten.
Werfen wir noch einmal einen Blick auf die Autoindustrie und den weltweiten Chipmangel. Automobilhersteller verwenden Halbleiter für alle möglichen Komponenten – von Airbags bis hin zur Echtzeit-Informationstechnologie. Sie könnten die Vorlaufzeit verkürzen, indem sie Chips dort, wo sie weniger wichtig sind, durch leichter zu beschaffende Produkte ersetzen.
Flexibilität und Reaktionsvermögen
„Schocks in der Lieferkette“, die sich auf die weltweite Produktion auswirken, treten nach Angaben von McKinsey alle 4 Jahre auf. Sie führen auch dazu, dass Unternehmen alle 10 Jahre 42 % der Gewinne eines Jahres verlieren.
Eine Kapazitätsplanung, die sich auf bewährte Prozesse konzentriert, mag die meiste Zeit über funktionieren. Aber wenn Sie mit plötzlichen Herausforderungen in der Lieferkette konfrontiert werden, ist Flexibilität entscheidend. Dies gilt insbesondere für Unternehmen mit geringen Gewinnspannen. Denn nur durch Flexibilität kann die Produktion aufrechterhalten und damit Ihr Unternehmen über Wasser gehalten werden.
In jedem Fall sollten Sie nicht in Panik geraten. Veränderungen können auch Vorteile mit sich bringen. Und letztlich lässt sich aus allem Lehren ziehen, die Ihnen dabei helfen, schneller auf bestimmte Situationen zu reagieren, um so für die Zukunft gewappnet zu sein.